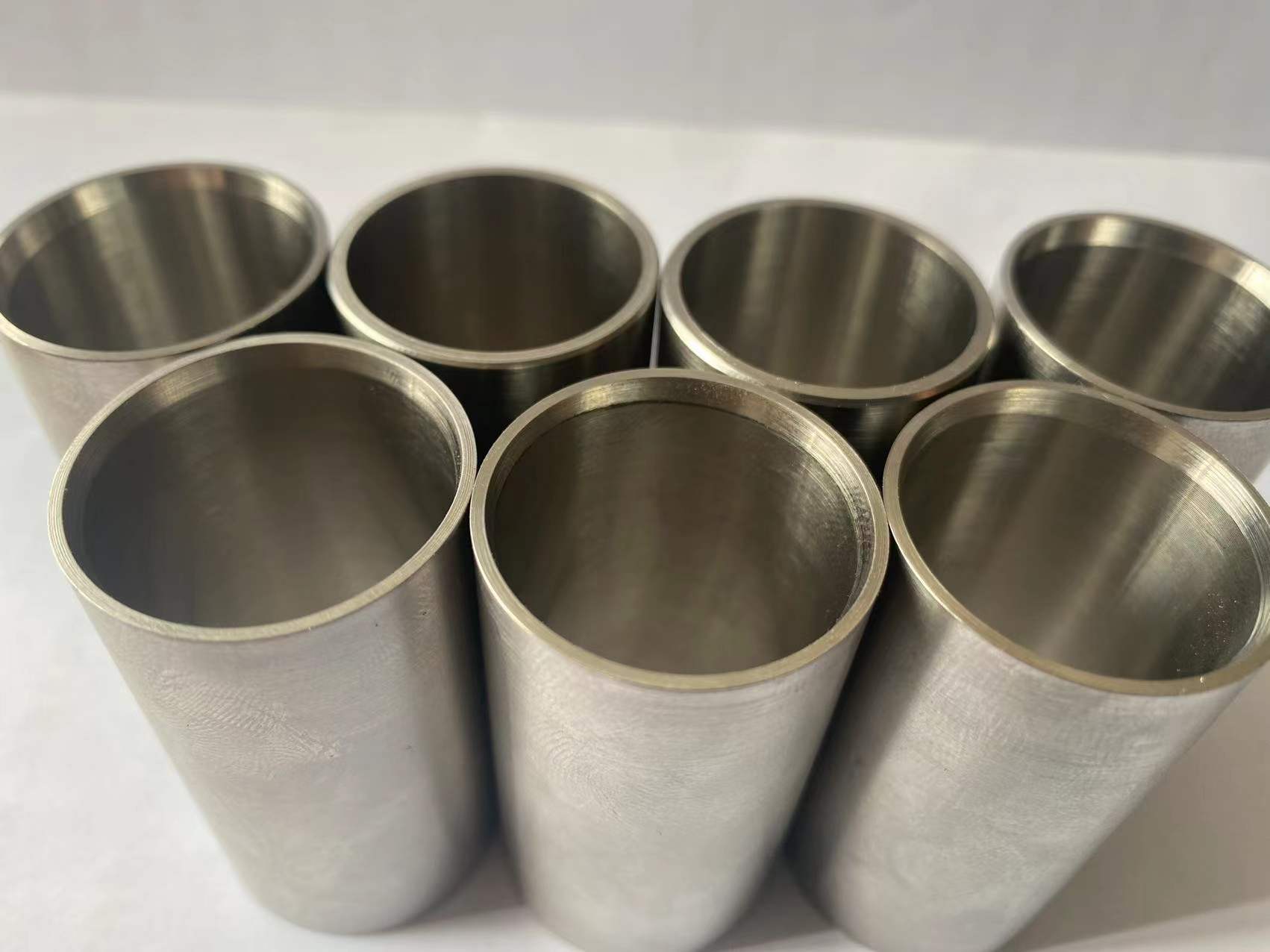
Inside the tomb of the pharaoh Tutankhamun (Tharakhatu), who ruled from 1361-1352 BC, is a small glass object with dark blue and cobalt. Cobalt blue was known even earlier in China and was used in pottery glazes. In 1730, the Stockholm chemist Georg Brandt became interested in the dark blue ore of some local copper mines, which he eventually proved to contain a hitherto unrecognized metal, which he gave to him by the Germans. The name of the ore cursed by the miners. Sometimes mistaken for a silver mine. He published his findings in 1739. Over the years, his claim that he had discovered a new metal was questioned by other chemists who said his new element was indeed a compound of iron and arsenic, but was eventually recognized as an element itself. Cobalt based alloy As a whole, cobalt-based alloys can often be described as wear-resistant, corrosion-resistant and heat-resistant (strong even at high temperatures). As a whole, cobalt-based alloys can often be described as w
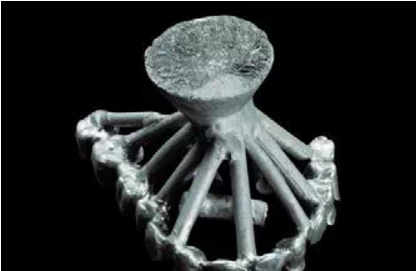
Dissatisfaction with casting results often prompts us to rethink our workflow and improve our original machining methods. The series of casting tests carried out in this paper resulted from the fact that when a particularly large pontic was cast using remaniumstar alloy, although the surfaces of the individual crowns were smooth, the majority of the pontic units were rough. Overheated alloys cannot be used during casting for large fixed bridges. The design and placement of the sprues adopts the traditional method: the sprue with a diameter of 3mm is used for the crown, the 3.5mm sprue is used for the bridge, and the 5mm is used as a transverse sprue to connect these sub-sprues. The diameter of the main sprue is 4mm. In the following, it will be described in detail what methods and steps are used to obtain a smooth and uniform surface of the casting. Preparation for casting test A prerequisite for smooth casting surfaces is the use of fine-grained embedding materials, such as remaCC for
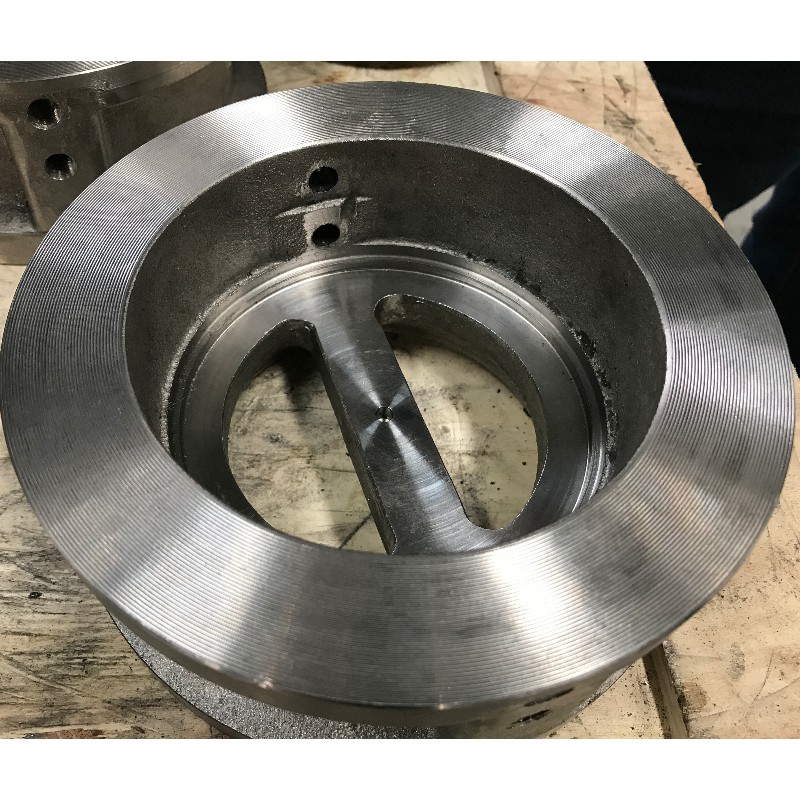
HC276 is known for its excellent corrosion resistance in various extremely aggressive media and harsh environments. It is a real super alloy among high nickel chromium molybdenum materials and is considered an outstanding alloy in the chemical industry. It can resist many of the harshest media encountered during chemical processing, including reducing and oxidizing acids. It has excellent resistance to sulfuric acid and hydrochloric acid, as well as excellent resistance to phosphoric acid. Controlled amount of tungsten and very high molybdenum content (up to 17%) C276 has excellent resistance to stress corrosion cracking and pitting corrosion. The seawater resistance of alloy C276 is also almost unparalleled, especially under cracking conditions, which can cause erosion of other commonly used materials, such as 316 stainless steel, 6MO stainless steel and Monel alloy. Hastelloy C276 is also favored by the oil and gas industry due to its ability to handle "sour" natural gas and th
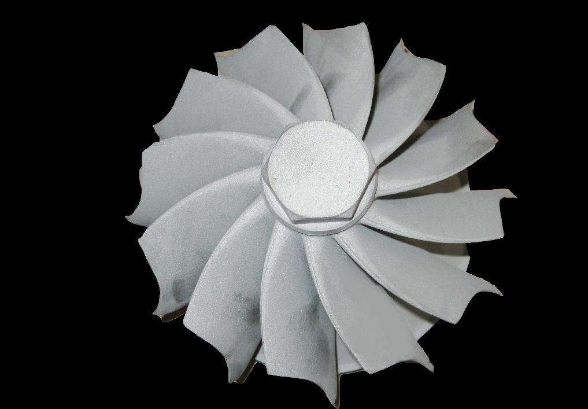
Gas turbine blades have to resist severe conditions such as elevated temperatures, high centrifugal forces and oxidation. Nowadays directional solidification (DS) and single crystal (SX) methods are used to cast the blades because conventional casting methods create superalloys with unsatisfying high-temperature properties caused by the equiaxed grain structure. Conventionally casted superalloys failed at the grain boundaries because of thermal fatigue, oxidation and creep. Grain boundaries are places for failure initiation. The alignment or elimination of these improves creep strength and ductility at high temperatures. To cast turbine blades is very complicated. Simplified, a mould is made by pouring a ceramic around a wax model of the blade. Then the wax model is removed and the mould is filled with the molten metal. Directional solidification (DS) The directional solidification of superalloys was introduced in the sixties.The grain boundaries are aligned parallel
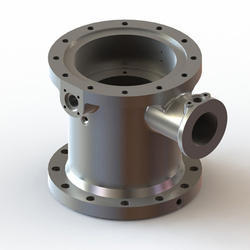
In600 UNS NO6600, W.Nr.2.4816, alloy600, NA14 Alloy 600 is a nickel-chromium-iron-based solid solution strengthened alloy with good high temperature corrosion and oxidation resistance, excellent cold and hot processing and welding process performance, and has satisfactory thermal strength and high plasticity below 700°C. The alloy can be strengthened by cold working, or it can be connected by resistance welding, fusion welding or brazing. Corrosion resistance Alloy 600 has corrosion resistance to various corrosive media. The composition of chromium makes this alloy have better corrosion resistance than nickel 99.2 (alloy 200) and nickel 99.2 (alloy 201, low carbon) under oxidizing conditions. At the same time, the higher nickel content makes the alloy have good corrosion resistance in reducing conditions and alkaline solutions, and can effectively prevent chlorine-iron stress corrosion cracking. 600 alloy has good corrosion resistance in organic acids such as acetic acid, acetic ac
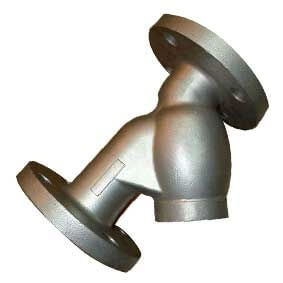
Nickel alloy is an alloy with nickel as the main element, which can be used in different parts of pipelines and industrial valves, such as valve bodies, valve covers, balls, valve seats, valve stems, bolts, springs, etc. Valves are part of a piping system and they are defined as components used for different purposes in a fluid flow. These purposes may involve stopping/starting flow, controlling flow, diverting flow, preventing backflow and releasing pressure [1] [2]. Figure 1 shows a ball valve which is a rotary valve in which the spherical closing member is rotated 90° to engage or disengage the port hole of the valve [2]. The ball in Figure 1 engages the through hole, thereby keeping the valve open. Figure 1. The ball valve is in the open position. Introduction of valves and components The different parts of the valve mentioned in this article are defined as follows [3]: Valve body: The valve body-also known as the valve housing-is the most important
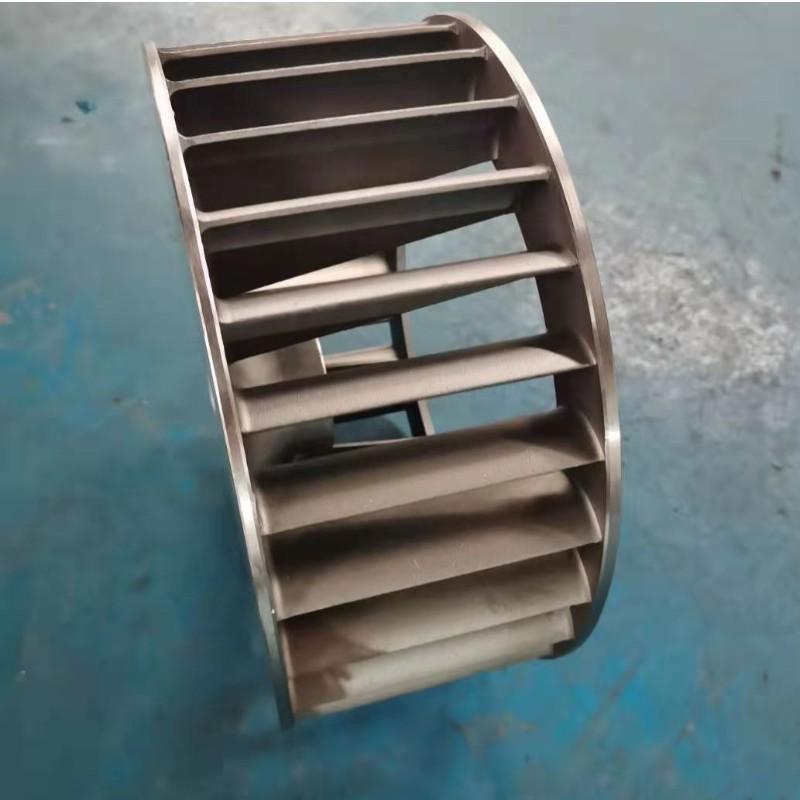
Alloy 713 is a precipitation hardening nickel-chromium-based casting alloy. It has excellent strength performance up to 1800ºF (980ºC). The alloy has good casting properties, and has excellent oxidation resistance and thermal fatigue resistance. The high-temperature strength and ductility of its alloy make it suitable for use as blade materials and first-stage blades for jets, guide blades for industrial turbines, forging dies, extrusion dies and die-casting dies. The alloy is actually a cast alloy and is not easy to forge. This is largely due to the need to put a large amount of precipitated elements into the solution before forging. On the one hand, high temperatures are required to achieve this solution, on the other hand, the precision forging temperature itself must be quite high. We must not forget the high-temperature strength of this alloy. Even with good high-temperature ductility, the hot working process will be difficult. The alloy may be forged between 2200 /1900&
825 alloy is sometimes referred to as super austenitic stainless steel and is the long-term service pioneer of nickel-iron-chromium alloys. Together with molybdenum, copper and titanium, this alloy will provide excellent corrosion resistance for a broad base in harsh environments. It has good resistance to stress corrosion cracking, and the high nickel content used in combination with copper and molybdenum makes it excellent resistance to reducing environments (such as environments containing sulfuric acid and phosphoric acid). The chromium content in the alloy resists various oxidizing substances (such as nitric acid), while molybdenum also helps resist pitting and crevice corrosion. The alloy will also maintain its strength at low temperatures up to 400°C and higher. It is widely used in the chemical processing industry, but due to its excellent resistance to corrosive environments (especially seawater), it has become an excellent material for the offshore industry. The only disa
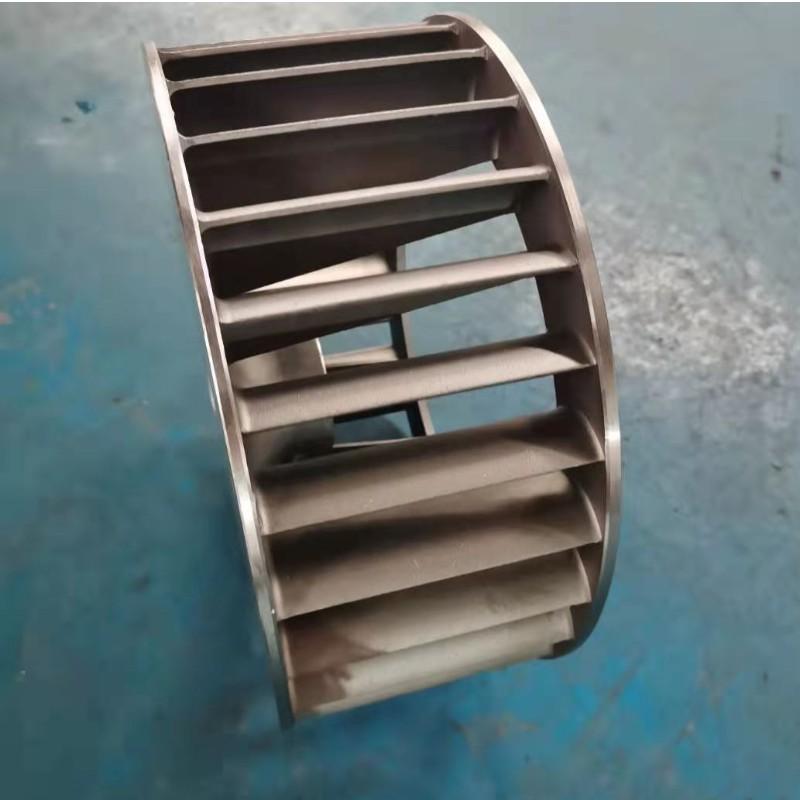
At the beginning of the 21st century, the economy and aviation market suffered severe crises, leading to the development of more efficient products by aircraft and engine manufacturers. The new generation of aircraft has improved aerodynamics, increased the use of composite materials and new aluminum alloys, and new manufacturing processes that help reduce weight. Aeroengines provide some of the most demanding applications for structural materials. Modern turbine engines operate at high temperatures and pressures, and engine components are often affected by destructive corrosion, oxidation and erosion conditions. These engines convert fuel energy into propulsion thrust. In the past few decades, higher engine performance has been achieved by increasing the turbine gas temperature and increasing the efficiency of each engine stage. Since the development of gas turbine engines for defense jet aircraft, the application of materials at high temperatures has been studied. The term superalloy
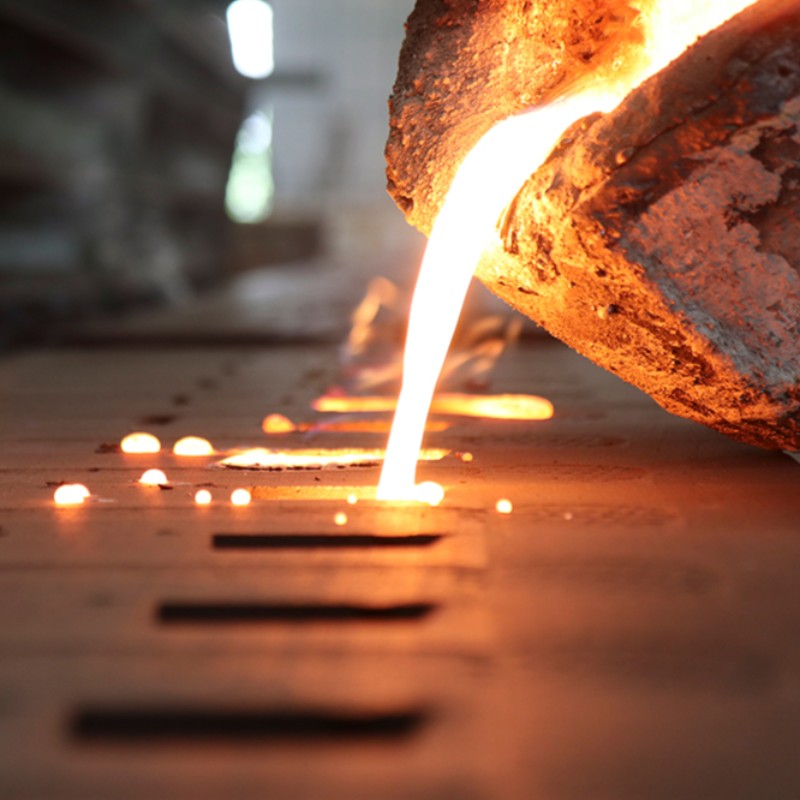
Invar 36[1], also known within the industry as Nilo 36[2], is a nickel-iron superalloy known for its low coefficient of thermal expansion. Containing 36% nickel, it maintains nearly constant dimensions as well as good strength and hardness over a wide range of temperatures. Invented in 1896 by Swiss physicist, Charles Edouard Guillaume, Invar was created as a low-cost solution to a meter once made of platinum and iridium. Guillaume’s work led to the discovery of a fairly inexpensive iron-nickel alloy—a steel-like material—that expands very little when heated. He named the alloy Invar because it was almost unchanging or "invariable.” Invar [3] is typically machined, but what many people don’t know is that it can be cast. Invar 36 Success We have developed and manufactured Invar36 castings a long time ago. Due to the confidentiality agreement, we cannot disclose the customer’s name, but what we
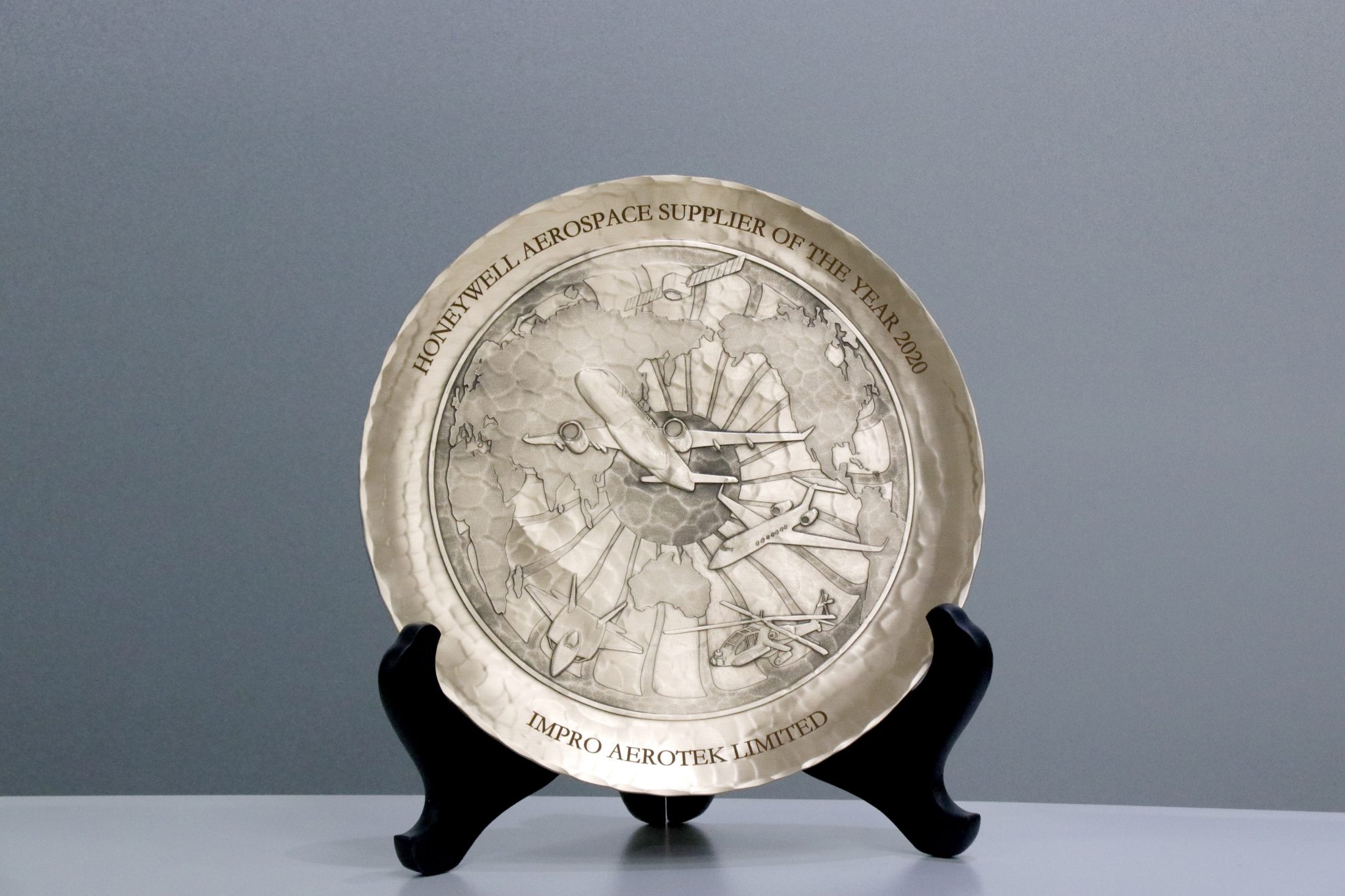
test